Tricky, tricky… Showing these weird tentacles and having a grasp at this big bulging head at the same time wasn’t easy, but it was achievable with the magic of this little narcissistic trick call a selfie. So here’s a triple portrait of Aimsee.
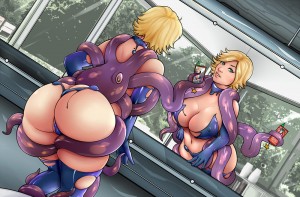
Cool bonus: the WIP pics courtesy of the artist.
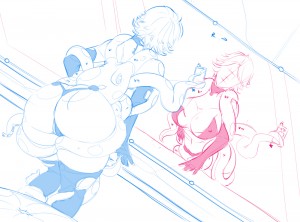
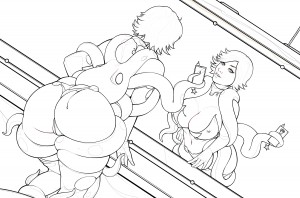
Want to join Arteria for commission? Go to Hentai Foundry to find how. Follow the link at your own risks.
(NSFW) http://www.hentai-foundry.com/user/Arteria/profile
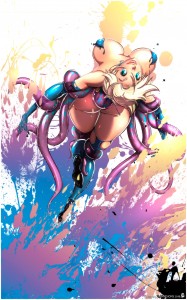
I’m always really happy about the fact that artists accept to work with me on my OC and other stuff related to my projects. Even though I’m not commissioning xxx artwork, I don’t mind working with talented artists, men and women, who give into it. Talent is talent and to each his own.
It was a pleasure chatting with Kamina. I really liked the way he made artistic suggestions for my piece. My requests are usually pretty rigid, so that was a nice change. It’s never easy for an artist to translate someone else’s vision into an actual artwork and to give life to your idea. Thank you, sir!
Kamina’s NSFW website (Wait, mine isn’t SFW either :S)
Go check that out !
http://artofkamina.com
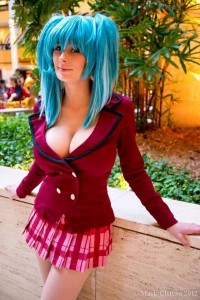
Tengo una buena noticia para mis amigos de México: soy una invitada por Megacon: Héroes y Villanos, 03-04 Dic’16 Mérida, Yucatán, Centro de Convenciones Siglo XXI ¡Y mi amiga la famosa cosplayer Vegas PG tambien!
I’m a cosplay guest for Megacon: Héroes y Villanos in Mérida, México, on December 3-4 2016. And guess who’s a guest with me? My lovely friend Vegas PG! Can’t wait to see you all there! And of course, I’ll stay a little longer in Mexico to enjoy the sun and the beaches!
http://www.megaconmid.com/

Great news! I’m adding one more convention date to my schedule in October and this time, it’s for a convention in the USA. I’ll be received as a cosplay guest for MegaCon Tampa Bay on October 28-30! Looks like I’ll celebrate Halloween under Florida’s sun this year!
http://megacontampabay.com/
Sitting on a spider
So we had the spider’s body holding by itself on its legs. That was very encouraging. And we had figured out a solution to the assembling/disassembling problem. This step was certainly the most complicated step from the whole building process and we were released that it was done. However, more challenges were waiting for us.
One of the questions that people asked me the most was: ‘Where are you gonna put your legs? Will they be hidden inside the spider’s body?’ On some of the drawings, you can see that the human part of Rachnera is attached to her spider body in a way that we couldn’t reproduce.
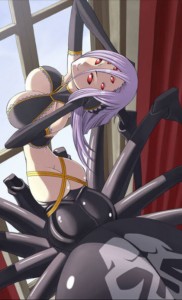
Even if my legs would have been hidden inside the body, there’s no way I could have kept my body in that angle for many hours in a row during the convention. The only logical solution was to have me sitting on the body. But what would we do with my legs? When you look closely at other Rachnera pics, you can see that she does have shorter ‘legs’ that are actually called ‘pedipalps.’
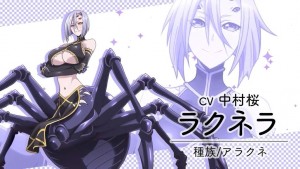
We thought that the best solution was to disguise my legs as the spider’s pedipalps. Making latex leggings for the costume would make my legs look as slick and shiny as the fiberglass spider body that would be shiny because of the automotive paint. The latex would imitate the spider’s ‘skin texture’ perfectly. But how would we integrate my feet in the pedipalps design? I tried various pointy high heel shoes, but it would always, in the end, look like shoes. It would have been disapointing to work that much on a fiberglass body to finally wear my Rachnera costume with simple shoes. So my friend and I built these fiberglass leg pieces that would cover my feet and give them a different shape. Of course, my legs would remain longer than Rachnera’s pedipalps, but at least, they would be covered by the same material than the rest of the structure, creating a camouflage effect.
Now that we knew that my legs wouldn’t be hidden inside the body and that I would be sitting on the body, we had to build my seat. It would be easy to create a fiberglass seat that would be part of the structure itself. However, it had to be a comfortable seat because I would have to stay there for a long time. Fiberglass remains fiberglass, not very comfortable, so the least we could do was to make sure that the seat would be… sculpted to fit my booty. I thought of older tractor seats. They had type of an ‘ergonomic’ shape. Remember that box containing the metal plate where the legs would be boalted? We cut a ‘seat’ shape in that box and sculpted a styrene lid. I would literally be sitting on the lid of the box giving us access to the legs’ assembling mechanism. On the next picture, notice the boalts coming out from under the seat, where the legs are fixed.
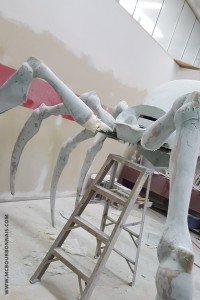
Then I tried to sit on our first attempt of seat. Since my legs were dangling off the edge, I had to hold my body to keep my balance. Otherway, I would fall down. It was clear that I couldn’t force my back and thighs muscles like this for many hours. We had to find a way to support me, to keep me on the seat. So we added that ‘bump’ in the middle front of the seat to support my crotch and keep my body in balance. It helped a lot. Plus, that part of the seat would be hidden by Rachnera’s loincloth. It was a good idea. But I still had to force my thighs muscles because the weight of my legs dangling off the edge of the seat was still pushing me down, making the under part of my thighs pressing very hard against the seat. After a couple of minutes, my thighs were numb already. And I wasn’t even wearing the fiberglass leg pieces that would add even more weight on my legs. That seat was far from being comfortable. That would be a bigger challenge than we had thought.
I suggested to add something on the front of the seat to support my legs as much as possible. We added 2 pads of EVA foam that we covered with fiberglass and integrated to the seat. If you look closely to the next picture, you’ll see these 2 little shapes in the front of the seat that we designed expressly to support my thighs. It wasn’t perfect, but I felt like it was as close as it could get to a ‘comfortable’ seat. We sanded and finished the edge of the seat so it wouldn’t hurt me. If we would have been building this for another model or cosplayer, I don’t think we coud have expected another girl to sit on this for a long time without feeling pain. But since we were building it for me and since I’m pretty resistant to muscle pain, I knew that I could stand it for the time of the convention. Anyway, we had to move on and we had no other choice. I would sit there and stay there no matter what.
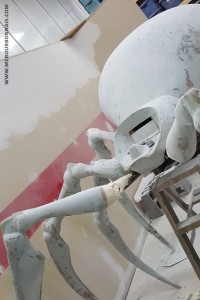
See the window wall on picture? Just so you know, that’s where my sewing room is. My sewing room is on the mezzanine floor in my workshop. Thanks to the window wall, when it’s summer time and when I work with the garage door of the workshop open, I can see outside even if I’m working in my sewing room. I love it!
Enough for today! Be ready for Part 6 of my making of blog! I’ll explain how the legs’ assembling mechanism was hidden by an intricate custom made lid.
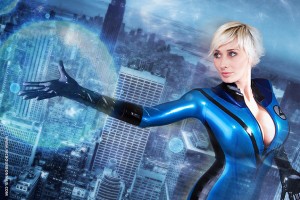
J’ai grand plaisir à annoncer que je serai de retour au Comiccon de Québec en tant qu’invitée cosplay les 22 et 23 octobre prochains! Venez me voir, ainsi que les autres invités, au Centre des congrès de Québec! J’aurai un tout nouveau costume que je dévoilerai bientôt. Pour plus d’information, consultez le site du comiccon:
http://www.comicconquebec.com/fr/accueil/
It’s a real pleasure for me to be received as a cosplay guest for Quebec City Comiccon this year! Come to meet me at the Québec City Convention Center on October 22-23. I’ll have a brand new costume that I will soon announce online! Fore more info, visit the comiccon’s website:
http://www.comicconquebec.com/en/home/
Rachnera’s legs: the magical assembling process
I’m showing you that picture of the spider’s body again because there are other details I want to point out.
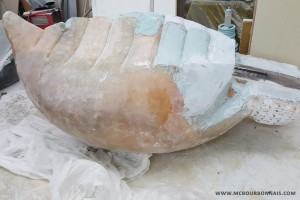
You can see that we had started applying batches of auto body filler all over the spider’s body. Experts will apply it more evenly. I do my best, but some intricate shapes are harder for me to cover evenly. The more little bumps, the more sanding I’m gonna have to do. At least, auto body filler is easy to sand. Easier than fiberglass. To apply body filler, I use a large variety of spatulas: rubber ones, plastic ones, metallic ones.
You can also notice a large metallic plate that comes out from the spider’s body and continues on the half sphere shape which is the front part of the body. The holes in that plate are where the legs will be boalted. Another half sphere fiberglass shape will be assembled there to cover and hide the top part of the legs. This second half sphere is removable because we need to have access to the legs to assemble and disassemble them. Now you can see that the 8 legs will come from the front part of the spider’s body. The biggest part of the body has no leg under it to support it. Just like a real spider. Which means that we needed the metallic support in the 4 big legs to be very strong.
For the 4 bigger legs, we used a gigantic round tubing, 3’’ of diameter, 1/8’’ of thickness. It was probably way more than necessary, but since I would spend hours sitting on that structure, and since the 4 legs had to support all the weight of the spider’s body, we wanted to make sure that it would be super strong. The round tubings were bended and welded to follow the shape of the bigger legs. You can see on the next picture how the tubing follows the shape of the original template and of the final fiberglass leg.
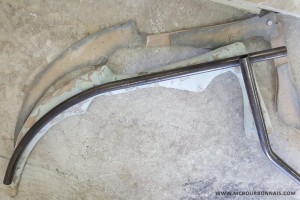
Wait. Yes, the leg is covered with fiberglass and the metallic structure is outside. Right. To insert the metallic structure inside the big legs, we had to cut them in halves with a buffer (which means fiberglass dust, awful step) and to take off the styrene and MDF template from the legs to keep only the empty fiberglass shell. Then we could put the round tubing inside and we patched the legs together again using the same method explained in my previous blog (see Part 3.)
Let’s take a look at the spider’s body holding on the 4 metallic tubings. Before going through the whole process of inserting the metallic tubings inside the legs, we wanted to make sure that they would really support the body. It worked well. Notice how the legs come out from the front part of the body. And notice how the spider’s belly was well sanded at that point. :) From sanders to single sanding paper sheets, anything you can think of that was created to sand, we used it. And we sanded a lot.
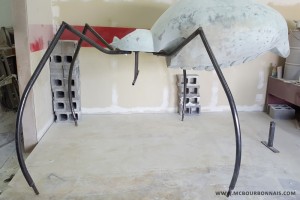
We were in the process of developing a concept that would allow us to lift up the spider’s body and install the legs. That body, even empty, was way too heavy to be held in the air by a few people while someone else would install the legs. Plus, its round shape was making it very hard to manipulate. And we knew that we couldn’t count on a 15 people team to help us installing the spider at the booth before Anime Expo. My friend and I really had to create a concept that would make the assembling and disassembling process doable by 2-3 people.
The most obvious way was to use the already existing metallic plate hidden in the spider’s belly, where the legs are boalted, as a part of our assembling/disassembling structure. There are 8 holes in the plate, one for each leg, and we used these holes to temporary fix the removable sturcture that would allow us to fix the spider’s body in its transportation box and to lift it up to assemble the legs. I’m skipping a couple of steps there, because it was later in the finishing sanding process, but I want you to notice, on the next picture, the metallic structures on the floor.
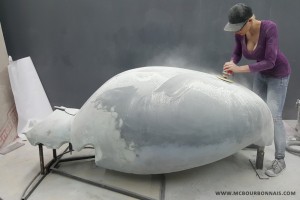
Before any of you make any comment about the fact that I’m not wearing a dust paper mask while sanding, please read Part 1 of this blog.
As it is on the picture, the metallic folded triangle and the metallic piece coming out from the spider’s tail allowed us to boalt the spider’s body to the bottom of its transportation box. See how we boalted it to the floor while we were sanding it. It was fixed the same way in the transportation box. To assemble the legs to the body, we had planned to take off the walls of the box and to let the tail of the spider boalted to the bottom of the box. We would then unfold the front part of the metallic structure, the triangle part, which would lift up the front part of the spider’s body, allowing us to fix the 2 first big legs. (I’ll share a picture of that step later, while I was actually installing the spider before Anime Expo.) Then, we could unboalt the tail from the bottom of the box, take off the metallic triangle from the front of the spider and fix it to the little part coming out from the tail, which would allow us to lift ut the back part of the spider’s body. At that point, the front of the body would hold on the front legs and the back, on the triangle metallic structure. We would then be able to boalt the 2 back legs, take off definitely the assembling structure pieces and fix the 4 remaining legs. It was a real engineering challenge to develope that process and when I think about it, I can’t believe that without any official engineering knowledge, we came up with that idea. And most importantly, I’m impressed that it actually worked. It was so much improvisation, but we had no choice, it had to work.
We’re getting closer and closer to see Rachnera alive! Watch for Part 5 of my blog to learn more!
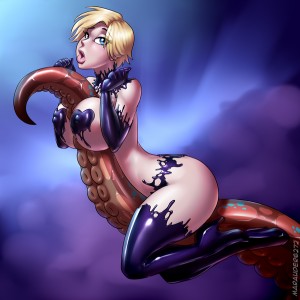
What a lovely surprise I had when I looked at my mails today! A message from an artist, Ian MacKey, or Marauder6272, who sent me this funny fanart of my OC, Aimsee! I can’t tell you how happy I am that people have been appreciating Aimsee so much since I introduced her. I had only positive comments about her and I’m looking forward to presenting you more of Aimsee in the future!
You can see more of Marauder6272’s work on his deviantart: http://marauder6272.deviantart.com/
Body filler and patience: how to make fiberglass feel and look as slick as glass
After the legs, we covered the spider’s body with fiberglass. Since the body was so big, we could use big squares of fiberglass mat instead of small pieces. However, the bigger the fiberglass mat pieces are, the more chances you have that there might be air bubbles trapped between the layers. To avoid air bubbles, you can use that metallic roller that has the shape of a paint roller without the sleeve. You roll it over the soaked fiberglass mat or cloth and then you make sure that all the air bubbles will go away. Covering the back of the spider’s body was pretty fast. Covering it’s belly was way longer. Rachnera has kind of a large textured stripped pattern on her belly that was very long to cover with fiberglass, but mostly, it was long to finish with body filler and to sand. On the next picture, you’ll see the spider’s body on its back. The part on the top is its belly.
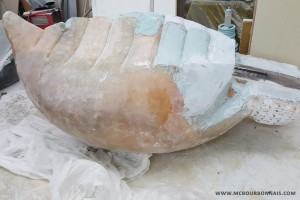
The amber colored thing is fiberglass. It has the color of the polyester resin I use. This is how fiberglass looks like before the finishing process. The blue product is the auto body filler. Body filler exists in many colors. It takes the color of the hardener you mix with it. There are different types of auto body filler. Some very rough body filler can be used to correct the shape of a fiberglass object and to fill up the fiberglass cloth texture. Very fine body filler with a super slick texture is used at the end for the finishing sanding to fill up small holes. The last, tiny holes will be filled up with the primer coat.
As I said, before you apply body filler, you can see all the texture of the fiberglass mat or cloth. If you want fiberglass to be as slick as glass and to have its famous shiny look that we love so much, you have to cover it with body filler and to sand it a lot. You don’t want to sand fiberglass. You want to sand body filler. Fiberglass dust is what is so itchy. Whenever you need to cut or buff a part of fiberglass, that dust is THE worst part of working with fiberglass. Fiberglass dust goes everywhere: on your clothes, on your skin and it itches so much that you wish you could rip off your own skin to stop it from itching. Water won’t completely remove the dust from your skin. Hot showers make it worst. It’s recommended to take a cold shower and to use a washcloth to wash your skin when you have fiberglass dust on you. That’s why you have to wear long clothes to protect your skin when you work with fiberglass. I’ve seen guys using tape around their wrists to fix their sleeves to their gloves in order to keep fiberglass dust from entering inside their shirt. Yes, it’s that bad. As much as you can, avoid to sand or buff fiberglass. Add an even coat of body filler everywhere and sand the body filler. Since I’m not a fan of cold showers, I always wear long sleeves when I work with fiberglass. Loose clothes are also more comfortable, because they don’t touch your skin and then you feel less the fiberglass dust that went on your skin. I just bought a product called ‘liquid gloves’ that is kind of a cream that you put on your hands and arms and that is supposed to create a layer that will protect your skin from paint and fiberglass. I’ll certainly try this product during my next fiberglass projet. Also, no need to repeat that wherener you’re using polyester resin and fiberglass, you have to wear a respirator mask.
Like a glass snowball
Speaking of fiberglass dust… We were concerned about the total weight of the spider. Weight influences the transportation fees and we wanted to make sure that it would be as cheap as possible for our clients, Ninja Division and Seven Seas Entertainment. What could we possibly do to take off some weight? We could empty the spider’s body and take off the styrene. Plus, we knew that we would have to assemble the spider by ourselves before Anime Expo. So we had to figure out a way to lift that big body and install the legs. The body would better be as light as possible. We definitely had to take off the styrene inside. Yes, styrene is light, but in such a big quantity, it becomes surprisingly heavy.
I remember when we were building Lug the robot. It took 4 bundles of 12 4’ X 8’ sheets of styrene to sculpt the whole robot. Some of you may remember that picture of me where I was making snow angels in sterene. There was styrene everywhere in the workshop. 48 sheets of styrene granules that I had to clean up even months after the robot was finished. That’s why I wasn’t so enthusiastic about taking off the styrene from the spider’s body, but I knew it wouldn’t be worst than the robot.
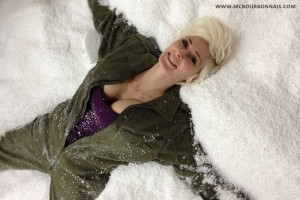
So we cut a hole in the spider’s body with a buffer (which is a good example of a step that produces fiberglass dust… itchy, so itchy.) You can see on the next picture the stacked sheets of sterene inside the fiberglass body.
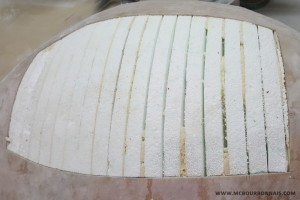
Then we took off all the styrene. It came out in bits and small pieces. It really took a while. And once again, there was styrene everywhere in the workshop, making it look like a glass snowball. Can’t remember how many garbage bags I filled up with all that styrene. Sorry, environment.
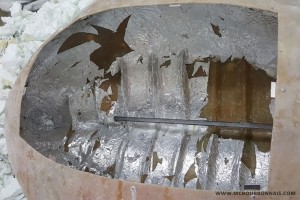
Now you can admire the empty fiberglass body. Notice how aluminium foil, that we had glued on styrene to protect it from polyester resin, stayed in the bottom of the fiberglass shell. It’s not important and doesn’t change anything since it’s hidden inside. It can stay there, it has no consequence. You have certainly also noticed a square tubing that crosses the spider’s body. It was welded on the other side to the metallic plate where the spider’s legs would be boalted. You can see it on the first picture of this part of the blog. Since that plate, located in the front part of the spider’s body, would support the whole weight of the body, we wanted to make sure that the plate wouldn’t come out from the body because of all that pressure. So we fixed the square tubing inside the body with more fiberglass. I’ll explain later how the legs were installed under the body.
Now that the body was empty, the last step was to put back the fiberglass piece that we had temporary removed. One of the only good sides of fibergalss is that it can be cut and patched as many times as you want and at the end, if you do a good job, it will not show. See how we put back the piece at its place, following the little notches we had made. We had to buff around the hole to make the surface lower in order to allow us to apply more fiberglass mat to hide the opening. If we would have only added more fiberglass mat on top of everything, we would have created a bump all around our piece that we are actually trying to hide. At the end, body filler will cover everything and you won’t be able to tell that there was once a hole there.
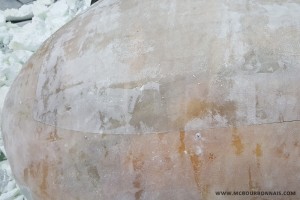
More body filler fun in Part 4 of my blog! And you’ll also discover how the spider’s legs were fixed to its body.
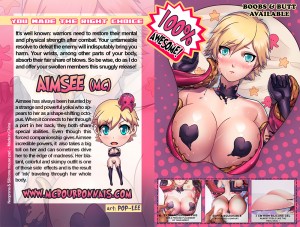
Introducing Aimsee, my original character! Discover her through some cute and sexy products like those super funny 3D mousepads. 2 versions available, boobies and booty. Your wrist will never feel the same! ;) You can order your Aimsee mousepads here.
It’s well known: warriors need to restore their mental and physical strength after combat. Your untameable resolve to defeat the enemy will indisputably bring you harm. Your wrists, among other parts of your body, absorb their fair share of blows. So be wise, do as I do and offer your swollen members this snuggly release!
Aimsee has always been haunted by a strange and powerful yokai who appears to her as a shape-shifting octopus. When it connects to her through a port in her back, they both share special abilities. Even though this forced companionship gives Aimsee incredible powers, it also takes a big toll on her and can sometimes drive her to the edge of madness. Her blatant, colorful and skimpy outfit is one of those side effects and is the result of ’ink’ traveling through her whole body.
Artwork by Pop-Lee
http://pop-lee.deviantart.com/
http://pop-leeart.tumblr.com/